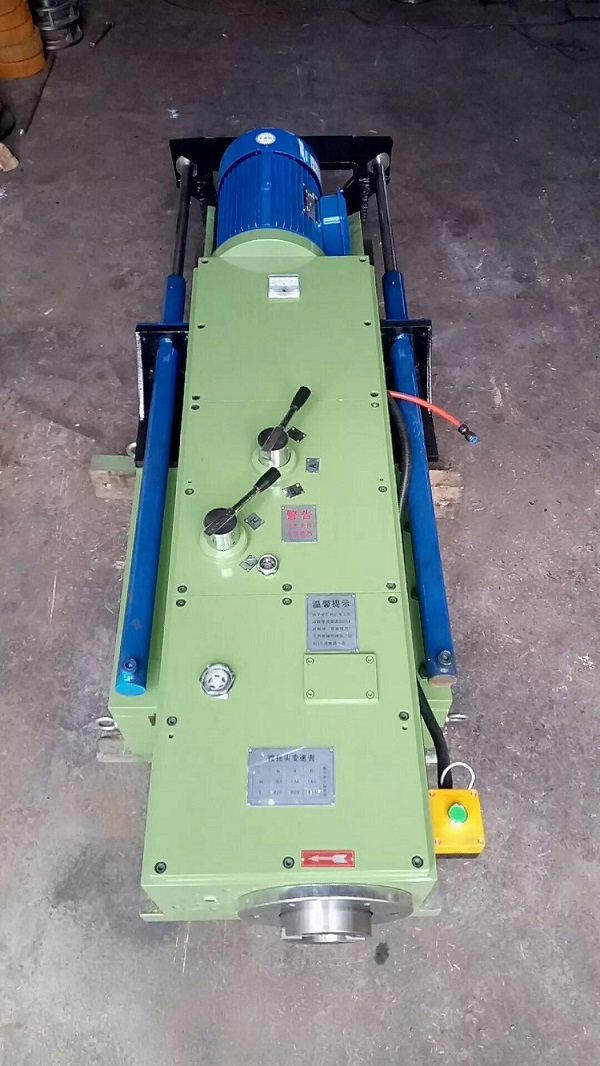
高密市振飛機(jī)械制造有限公司
經(jīng)營模式:生產(chǎn)加工
地址:山東高密市夏莊鎮(zhèn)河西村
主營:鏜銑頭,銑頭,動(dòng)力銑頭,數(shù)控銑頭,直角銑頭,萬向銑頭
業(yè)務(wù)熱線:0536-2758966
機(jī)械動(dòng)力頭-振飛機(jī)械-機(jī)械動(dòng)力頭多少錢
鏜銑頭,銑頭,數(shù)控銑頭
萬向銑頭具可換性
萬向銑頭主要為擴(kuò)大鏜床在實(shí)際工作中的加工范圍,即沒有銑頭只可加工一個(gè)工位,到安裝銑頭一次性可加工到8個(gè)工位,并且主軸可伸展100-150毫米。下面是銑頭的加工過程。
①操作者將要加工的零件放在工件臺的夾具中,在其它準(zhǔn)備工作就緒后,發(fā)出加 工指令。 ②工件夾緊后壓力繼電器動(dòng)作, 液壓動(dòng)力滑臺 (工作臺) 開始快進(jìn), 到位轉(zhuǎn)工進(jìn), 同時(shí)啟動(dòng)左和右 1 銑頭開始加工,加工到某一位置,立銑頭開始加工,加工又過 一定位置右 1 銑頭停止,右 2 萬向銑頭開始加工,加工到終點(diǎn)三臺電動(dòng)機(jī)同時(shí)停止。 ③待加工完全停止后,滑臺快退回原位,工件松開,一個(gè)自動(dòng)工作循環(huán)結(jié)束。 ④操作者取下加工好的工件,再放上未加工的零件,重新發(fā)出加工指令重復(fù)上述 加工過程。
萬向銑頭主軸箱采用樹脂砂造型的高強(qiáng)度鑄鐵以及合理的不筋結(jié)構(gòu),剛性好、穩(wěn)定性強(qiáng)。工作臺拖動(dòng)采用大慣量交流伺服電機(jī)、配置高品質(zhì)滾珠絲杠和重載直線導(dǎo)軌,經(jīng)優(yōu)化設(shè)計(jì)擁有良好的定位精度及穩(wěn)態(tài)響應(yīng)特性。主運(yùn)動(dòng)采用寬調(diào)速交流伺服主電機(jī)、減速箱,使得主軸在低速時(shí)大扭矩輸出,萬向銑頭適合重切削,高轉(zhuǎn)速時(shí)的恒功率適合精加工。






數(shù)控機(jī)床臺灣銑頭回轉(zhuǎn)軸的定位夾緊方式
首先必須將所要加工件臺灣銑頭的全部信息,包括工藝過程、刀具運(yùn)動(dòng)軌跡及走刀方向、位移量、工藝參數(shù)(主軸轉(zhuǎn)速、進(jìn)給量、切削深度)以及輔助動(dòng)作(換刀、變速、冷卻、夾緊、松開)等,按加工順序采用標(biāo)準(zhǔn)或規(guī)定的程序指令編寫出正確的數(shù)控銑加工數(shù)控加工程序,然后輸入到數(shù)控設(shè)備的控制系統(tǒng)中,隨后控制系統(tǒng)按數(shù)控程序的要求控制數(shù)控機(jī)床對零件進(jìn)行加工。所謂數(shù)控編程,一般指包括零件圖樣分析、工藝分析與設(shè)計(jì)、圖形數(shù)學(xué)處理、編寫并輸入程序清單、程序校驗(yàn)的全部工作過程。
端齒盤式定位夾緊機(jī)構(gòu)具有固定角度分度定位功能,通過動(dòng)齒盤與靜齒盤的脫開、轉(zhuǎn)位和嚙合即可實(shí)現(xiàn)回轉(zhuǎn)軸的鎖緊和的分度定位。臺灣銑頭其zui小分度單位受齒盤的齒數(shù)限制,由于誤差平均效應(yīng),齒盤的齒數(shù)越多,定位精度也越高,常用的端齒盤定位精度一般可達(dá)±2”以上。同時(shí)端齒盤還具有傳動(dòng)扭矩大、傳動(dòng)剛性好等特點(diǎn),設(shè)計(jì)中為了保證分度定位能夠提供足夠的扭矩和較高的保持剛性,通常通過液壓拉釘或碟簧等機(jī)構(gòu)在軸向方向上對端齒盤施加一定的軸向預(yù)緊力來鎖緊動(dòng)。
龍門銑頭裝配的過程
龍門銑頭裝配滾珠絲杠、氣動(dòng)拉刀,再加上伺服電機(jī)驅(qū)動(dòng),性能發(fā)揮一覽無余;側(cè)銑搭配V5型龍門銑,加裝新型獨(dú)li潤滑裝置,升降則仍然使用普通減速機(jī)進(jìn)行傳動(dòng),變頻調(diào)速更加方便;龍門銑床數(shù)控銑擁有的一鍵式三軸轉(zhuǎn)換數(shù)控系統(tǒng),能夠簡單實(shí)現(xiàn)編程與面板手動(dòng)操作二合一,快速便捷的實(shí)現(xiàn)機(jī)械加工;連著搭配,
機(jī)床作業(yè)前一定要確定刀具已經(jīng)夾牢,加工件同樣需要使用壓板、螺釘或是專用工具夾緊;工作前檢查好機(jī)床各部位,尤其是傳動(dòng)部分的運(yùn)轉(zhuǎn)狀況,機(jī)床擋板務(wù)必裝配得當(dāng);各種銑削工藝都需要按步進(jìn)行,尤其是粗銑過程.